Active Pneumatic Vibration Isolation System
DVIA-P Series
Designed for Semiconductor Metrology
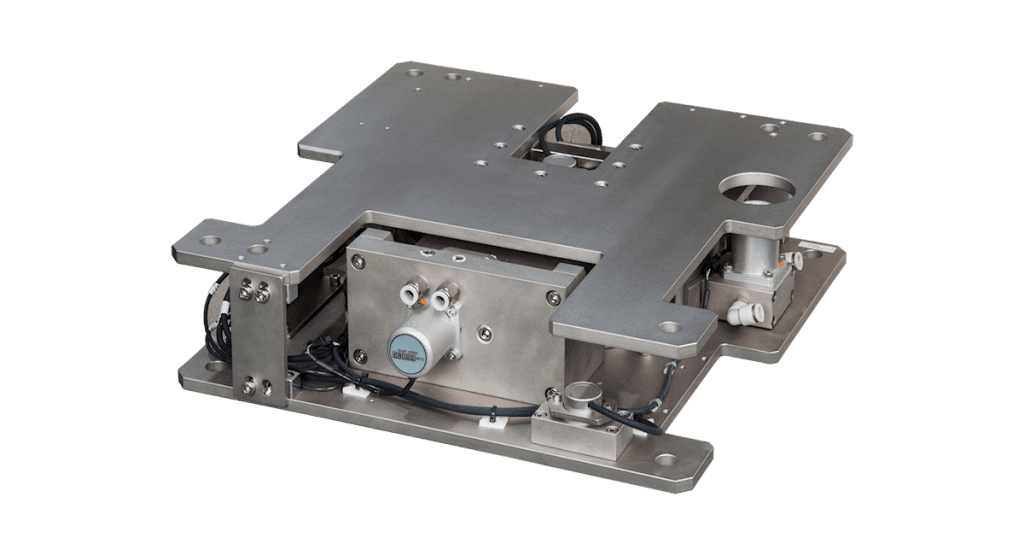
- Overview
- Features
- Performance
- Specifications
- Applications
- Resources
The DVIA-P series is the advanced active pneumatic vibration isolation systems, employing pneumatic servo valve actuators to
control low-frequency vibrations and stabilize semiconductor metrology equipment with ultra-precision motorized
linear stages. The DVIA-P series incorporate extremely sensitive sensors and powerful pneumatic servo actuators,
generating enormous force to counteract incoming vibrations from building floors and deliver
the ultra-fast settling time for nano-resolution imaging without any disturbances.
Superior Vibration Isolation Performance
The advanced feedback and feedforward vibration control algorithms are embedded in the DVIA-P series,
delivering 40 – 70% at 2 Hz in six degrees of freedom.
Designed for Semiconductor
Metrology Equipment
Based on analog input and acceleration data in real time, the stage feedforward control system in the DVIA-P series effectively
compensates residual vibrations caused by motorized linear stages. When linear stages travel with large acceleration
and mass, large displacement occurs,the acceleration feedback control of DVIA-P series minimizes the displacement,
reducing the settling time and improving the position accuracy of the system. Furthermore, if analogue outputs
of the stage position displacement acceleration that measured in real-time are connected to the controller,
the stage feed-forward system can be employed. The SFF system generates a force that is proportional to the stage
rotational moment and the stage vibration force, which can reduce the position displacement of the linear stage drastically.
10 μm Position Accuracy
The position sensors continuously measure the position of the isolation system and then maintains its the position
through a digital signal processor.As a result, the position accuracy of the system is significantly improved.Furthermore,
accelerometers instantly detect vibrationsoriginating from the floor or the moving stages,
then transmit the digital signalsto operate pneumatic actuators to cancel out the vibrations.
Powerful Pneumatic Actuators to Support Moving Stage Applications
The DVIA-P series is inherently stiffer than passive vibration isolation system due to the enormous force generated by
the pneumatic actuators. The pneumatic actuators generate the significant amount of force to support
the semiconductor / display metrology equipment with integrated motorized linear stages
Feedback & Feedforward Control Algorithm
If the isolation system has information about motorized linear stages in advance, the system can produce the force that equal in size to the force from dynamic linear stage motions in the opposite direction. As a result, the external force caused by the motorized linear stage is effectively minimized.
This feedback control system employs sensors and actuators to continuously detect vibrations which disturb the isolated payload, then reacts to minimize vibrations. The acceleration feedback system not only reduces from the floor but also effectively minimizes vibrations from the motorized linear stages.
When the isolated base is disturbed by vibrations, the position feedback measures displacement through position sensors that transmit signals into the digital controller. After receiving the signals from the sensors, the digital controller drives actuators to return its original position, improving the position accuracy.
The floor feed-forward system filters the floor vibrations in a predefined way. The feed-forward control system is utilized when there are known factors such as a force applied to the isolated base, the data of ambient vibrations and information about equipment that needs to be isolated. Unlike the feedback control system, the feed-forward system analyzes dynamic characteristics of the equipment and tunes the feed-forward gains by the trial and error method to operate the actuators.
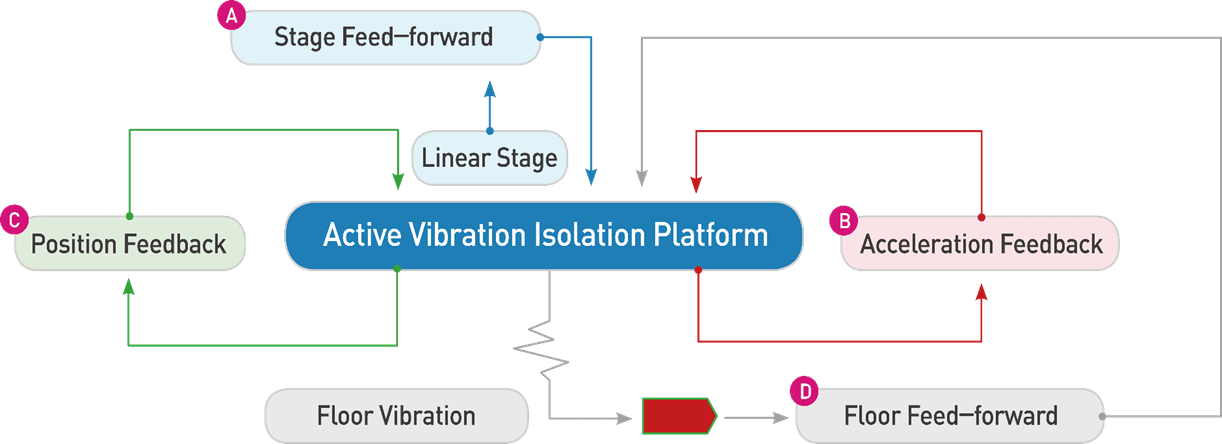
Smart Control System
A digital controller of DVIA-P series employs a A/D 19-channel 16-bit ad a D/A 10-channel 24-bit D/A
converterto obtain synchronous sampling of vibrations. The digital controller controls the system by constantly
calculating all sources of vibration, then transmitting signals to drive the pneumatic actuators.
Active Vibration Isolation
in All Six Degrees of Freedom
The DVIA-P series controls vibrations in six derees of freedom including, three translational degrees of motions
( X, Y and Z), and three rotational degrees of motions ( pitch, roll and yaw).
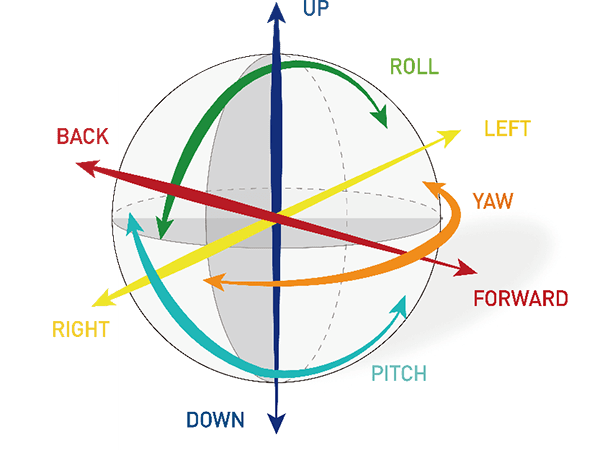
On-Site Tunting for Perfection
Floor Vibration levels vary with installation sites, surroundings, irregular events and various vibration sources. Therefore, we offer on-site tuning of the active vibration isolation system, performed by our experienced engineers to guarantee the maximum vibration isolation performance and customers' satisfaction.
40 – 70% vibration isolation at 2 Hz.
≥90% vibration isolation at ≥4 Hz.
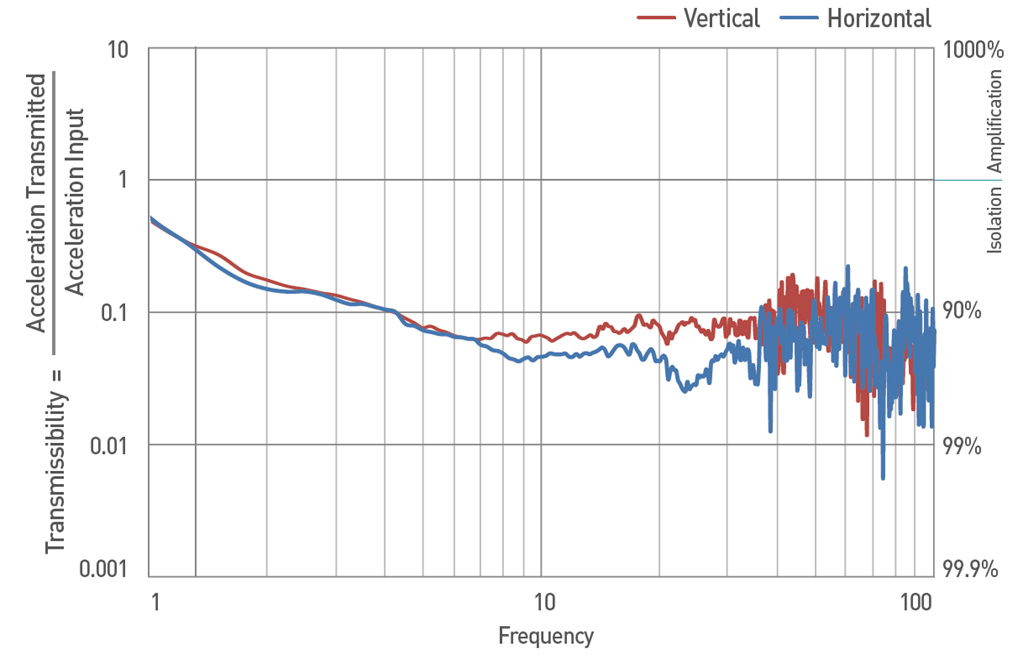
Model | DVIA-P550 | DVIA-P1000 | DVIA-P2200 | DVIA-P4000 | DVIA-P7000 | DVIA-P10000 | DVIA-P20000 | DVIA-P30000 | |||||||||
---|---|---|---|---|---|---|---|---|---|---|---|---|---|---|---|---|---|
Isolator Dimensions (mm) |
215 x 160 x 170 | 240 x 240 x 110 | 350 x 350 x 110 | 420 x 420 x 110 | 450 x 450 x 120 | 400 x 465 x 240 | 645 x 600 x 284 | 735 x 700 x 284 | |||||||||
Load Capacity (kg) |
270 – 900 | 500 - 1700 | 1100 - 3700 | 2100 - 7000 | 3600 - 12000 | 5000 - 17000 | 11000 - 38000 | 150000 - 50000 | |||||||||
Actuator | Pneumatic Servo Valve Actuator |
||||||||||||||||
Maximum Actuator Force | Vertical | 4400 N | 8200 N | 18000 N | 34000 N | 58000 N | 83600 N | 186000 N | 244000 N | ||||||||
Horizontal | 390 N | 780 N | 780 N | 1300 N | 2200 N | 2200 N | 5800 N | 5800 N | |||||||||
Degrees of Freedom | 6 degrees | ||||||||||||||||
Active Isolation Range | 0.5 - 150 Hz | ||||||||||||||||
Vibration Isolation at 2 Hz | 40 - 70% | ||||||||||||||||
Vibration Isolation at ≥4 Hz. | 90% | ||||||||||||||||
Input Voltage (V) | AC Single Phase 100 - 240 V | ||||||||||||||||
Power Consumption (W) | 100 W | ||||||||||||||||
Operating Range | Temperature (°C) | 5 - 50 °C | |||||||||||||||
Humidity (%) | 20 - 90% | ||||||||||||||||
Required Air Pressure | ≥ 0.5 MPa (≥ 5 bar) | ||||||||||||||||
Required CDA | 250 NL/min |